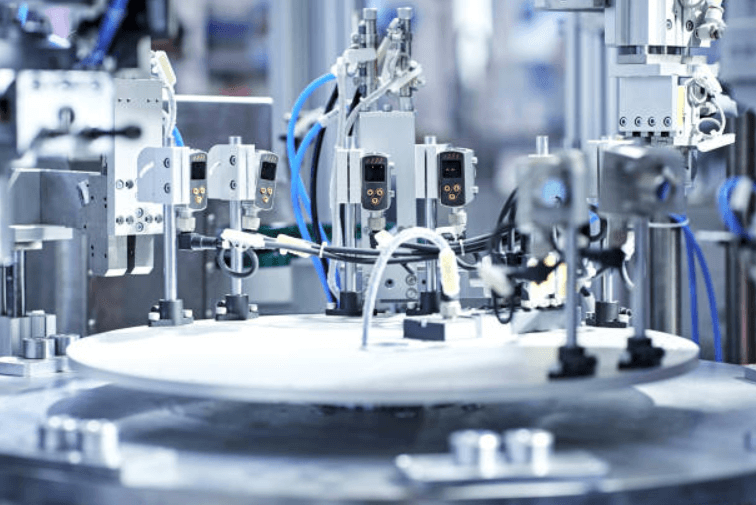
Capacitive vs. Inductive Proximity Sensors: Choosing the Right Option for Your Needs
Inductive proximity sensors are generally used in industrial automation to provide highly accurate, non-contact recognition of objects in several settings. There are two main categories of proximity sensors; capacitive proximity sensors and inductive proximity sensors, both different in the way they work. Technology selection is key in any industry but for an industrial automation services company it means identifying the difference between these sensors to advise the right choice to their clients. Tailor-made solutions will also improve clients’ processes’ outcomes and accuracy in automation systems for the companies. This article is a comparison between capacitive and inductive proximity sensors to enable you to make a decision in the event that you need to use either of them in your project.
What are Capacitive and Inductive Proximity Sensors
Capacitive and inductive proximity sensors are both types of non-contact sensor systems designed to detect objects, however, they work in different fashion for definite purposes. Capacitive proximity sensors sense variation in capacitance due to an object being nearby, and are suited to both metal and non-metallic objects like plastics, liquids, and powders. They can be used to sense through a non-conductive layer of glass or plastic and thus cover a wider area of use. Inductive proximity sensors on the other hand create electromagnetic fields and measure disturbances caused by metallic objects thus used in industrial application specifically for use in metal detection. These sensors are particularly useful where there may be mechanical movement and metallic object identification is important. In an industrial automation services company, the provision of these two types ensures that clients get differentiated services depending on their requirements for automating certain processes to increase precision thus improving on their efficiency. This makes them tools of paramount importance in attaining the best operational efficiency in automation systems.
See also: Creative 10×10 Exhibit Booth Ideas to Stand Out at Your Next Trade Show
Key Differences Between Capacitive and Inductive Proximity Sensors
When considering the capacitive proximity sensors against inductive proximity sensors the following aspects define the two. Metal and non-metal targets are both detectable with capacitive sensors, and the sensors can even measure through layers of non-conductive material such as glass or plastic. By doing so they are especially useful in sectors such as packaging, food processing and in pharmaceutical industries, where it is necessary for different materials to be identified. However, inductive sensors are used solely for capturing metallic targets with the higher accuracy but limited coverage distance. Due to their durability, they can sustain metal fabrication or automotive assembly environments where temperature changes and electromagnetic effects prevail. Capacitive sensors are best used for scoping up objects in clean environments that cover limited areas, whereas inductive sensors are perfect for rigorous industrial applications where they are likely to stay for relatively long times. For companies that depend on proximity sensors, such distinctions assist in the right choice for proper applications and acts as a guide in selecting the right sensor for specific settings to help it perform its best with little or no breakdown.
Applications of Capacitive and Inductive Proximity Sensors
Resistive and reactive types include capacitive and inductive sensors, and are employed in several industrial applications; each has unique functions. Inductive sensors find application in, for example, the packaging industry in operations that focus on recognizing liquids or granular substances, as well as in operations where there is a need for comprehensive exactitude in the sensing and rejection of non- ferromagnetic materials. They are also used in the storage systems in order to check the levels of powders or liquids with non-conductive containers and review the production flow. Intuitive sensors, on the other hand, are critical in metal cutting and automotive manufacturing where they are used to sense position and to monitor production lines as well as the correct positioning of metallic products. The durability of wheel loaders is also important for use in applications such as construction and mining wherein equipment must maintain peak performance under prevailing climatic conditions. These sensors are very important to make the operations safe and accurate in operation and other automated applications irrespective of the level of sophistication of the application. To an industrial automation services company it is essential to offer these sensors customized to meet the needs of different industries in order to ensure smooth integration and optimization of operations of the company’s customers from different sectors.
What You Should Know When Selecting the Right Sensor
Therefore selecting capacitive or inductive proximity sensors depends on several factors that define a successful application. The kind of material to be sensed is the most important factor here; capacitive sensors are actually ideal for material such as liquid or plastic and the inductive is ideal for metal. Environmental conditions are also an important factor; capacitive sensors are designed to work in clean and odorless environments while inductive sensors are designed to work in factory floors where temperatures can go high, there might be moisture or a lot of electromagnetic interference. The sensing range is a critical element, although capacitive sensors are suitable for variable detection distances while also inductive sensors are developed for high accuracy but with shorter distances. Consequently, the costs of operations, maintenance, and compatibility with other systems become essential factors to be considered when choosing a sensor. Through consultation with an experienced industrial automation services provider, industries will get the right sensor that [fulfills] enhanced performance and durability of the system. These considerations guarantee that the chosen sensor not only fits the present need, but also has potential to be scaled up in future.
Conclusion
To distinguish the correct capacitive vs inductive proximity sensor type out of all the given possibilities is critical in the automation industry. While capacitive sensors are widely used for measuring non-metal objects with great flexibility, the induc-tive sensors are characterized by high accuracy and stability when it comes to working with metal materials, as well as in conditions of increased aggressiveness. Both types of sensors apply their advantages in certain industries which makes them essential to use. The fact that industrial automation services companies deal with different industries makes it crucial that it provides both kinds of sensors as a way of satisfying competing needs. Therefore based on the analysis of material, environment, and sensing range, potential recommendations for businesses can be made. Selecting the appropriate proximity sensor is the initial course towards the achievement of increasing productivity, decreasing overall expenditures and providing for effective and reliable operation within industrial systems so as to provide for smarter forms of automation. New technologies are not only refined with these sensors to enhance current processes but also allow industries to integrate with future progressive techniques in automation technology.