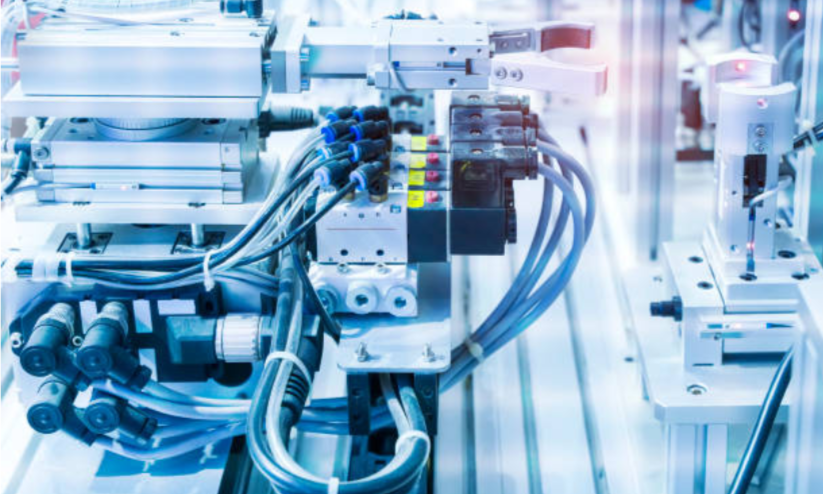
FRL Pneumatics in Industrial Automation: Making Compressed Air Work Harder for You
Compressed air keeps factory floor machines humming, from robotic arms to conveyor belts. But air straight from the compressor often carries dirt, water, and pressure spikes that can shorten a system’s life. That is why adding FRL pneumatics—Filters, Regulators, and Lubricators—is such a smart move for any plant. For manufacturers, packers, and precision-engineering shops, a sturdy FRL set-up keeps production steady and cuts unexpected repair bills.
In this post, we break down what FRL units do, tips for picking the right ones, and how companies like Omchele deliver dependable air-prep solutions that grow with your needs.
What Are FRL Units and Why Do They Matter?
FRL units—short for Filter, Regulator, and Lubricator—sit between the compressor and the tools, cleaning, steadying, and slicking the air heading into valves and cylinders. Each part tackles a specific job:
- The Filter catches dust, moisture, and oil mist that could clog or corrode equipment.
- The regulator keeps pressure steady, so machines get the power they need without endangering seals or piping.
- The Lubricator sprays a light mist that eases friction on moving parts and helps them last longer.
Pneumatic systems that skip proper air treatment end up coughing, sputtering, and grinding to a halt. Problems like plugs in the line, shifty pressure swings, and parts that wear out too fast pile on inefficiency, force extra repairs, and lose valuable production time. For any B2B firm that counts on air-powered machines, those headaches quickly bleed money and stall output.
That is why FRL units are far more than optional extras; they are frontline gear that guards every dollar spent on automation. Dive into FRL options built for heavy-duty factories right here, where Omchele shows off a wide range of filters, regulators, and lubricators tailored to suit almost any job.
A Quick Guide to FRL Parts and Their Jobs
Each component inside an FRL box has its own task, and knowing what each piece does makes it easier to build the air-cleaning chain your shop really needs.
Filter: The Front-Line Bodyguard
Filters snag dirt, dust, and pesky water droplets before they hit valves and cylinders. That job is vital in humid regions or when factory intake air drags in street grime. Miss this step, and a single clogged port can bring a whole line to a standstill. FRL filters come in ratings from 5 to 40 microns, each tuned to trap particles of different sizes.
Regulator: Keeping Pressure Steady
The regulator keeps air pressure steady downstream, no matter how much the supply side jumps around. Without that steadiness, actuators can jerk, safety risks rise, and automated machines lose their fine touch. In fast-moving or high-precision factories, a rock-solid pressure floor is not optional; it is the foundation of reliable work.
Lubricator: Adding Lifespan
Lubricators spray a fine cloud of oil into the airflow, greasing seals, pistons, and vanes before they even touch metal. Less friction means tools and cylinders run cooler, wear out slower, and cost the plant fewer repair bills. Clean shops, such as food lines, often skip the oil, yet in heavy-duty mills or assembly floors, the lubricator is a must-have.
Omchele, a recognized name in industrial automation, builds FRL blocks that snap together the way engineers want. Its modular sets slide into any lineup, are easy to service, and can be tweaked on the fly—perfect for B2B teams juggling changeable production runs.
See Also: Innovations in Furniture Hardware: The Impact of the New Anodizing Technology
Why FRL Sets Boost Factory Efficiency
When factories rely on many pneumatic circuits, a single set of FRL parts pays back more than better air quality. It touches output speed, machine uptime, product consistency, and even the paperwork needed to pass audits.
- Longer Gear Life: By catching grit first and adding oil last, FRL stations cut abrasion and ease the strain on moving parts.
- Energy Savings: By keeping air pressure steady, the system avoids running actuators at higher-than-needed levels. That small change trims air use and cuts energy bills.
- Better Product Quality: Even pressure helps machines behave the same way every time. That repeatability is key on lines where tiny tolerances make all the difference.
- Less Downtime: Clean, well-controlled air sparks fewer jams and surprise stops. Technicians can spend their shifts on planned checks, not chasing emergency repairs.
- Meeting Standards: Many sectors must prove their air meets strict rules. Solid filters plus good maintenance put companies in line with ISO and other certification demands.
And for firms that run plants on different continents, a global solution saves headaches. Omchele’s https://www.omchele.com/es/frl-units/ offers a range of units that can be standardized everywhere, streamlining training and spare-part stocks.
Tips for Picking FRL Units for Your Pneumatic Network
When B2B teams set out to sharpen their compressed-air setup, choosing the right FRL module means balancing technical specs with everyday needs:
- Flow Capacity: Check that the unit can pass the peak airflow, measured in CFM or L/min, demanded by all valves and tools downstream.
- Pressure Range: Match the FRL’s rated inlet and outlet bands to your system pressure so that devices get steady air, with neither over-stress nor lack of force.
- Port Size and Mounting: Before you buy, check your system layout and pick an FRL with matching pipe threads and the right way to bolt or clip it in place.
- Material Compatibility: In plants every shift exposes equipment to steam, chemicals, or salt spray, stainless steel or special coatings stop rust and keep the line safe for workers.
- Ease of Maintenance: Slide-out cartridges and open designs let crews swap parts or wipe them down fast, cutting downtime to minutes instead of hours.
- Integrated vs. Modular Units: An all-in-one manifold sits neat on the rail and cuts pipe runs, but a build-your-own stack lets you swap one filter, regulator, or lubricator without junking the whole block.
Omchele’s FRLs hit the sweet spot between ruggedness, low upkeep, and easy add-ons, making them the go-to choice for engineers and plant leads who want air-smart gear that grows with tomorrow’s automation.
Real-World Applications and Industry Use Cases
FRL pneumatics show up wherever air power drives production. Here are a few places you might spot them in action:
- Automotive Manufacturing: Smooth, steady pressure keeps robot weld guns and assemble arms firing without sputters or leaks.
- Electronics Production: Clean, dry blast protects tiny boards from dust or moisture while they come together on the line.
- Food and Beverage Processing: Stainless parts feed safe, oil-free air into fillers and sealers, so every bottle stays fresh and contamination-free.
- Aerospace Engineering: In testing cells, pinpoint regulators let teams gauge and adjust wing and engine parts down to millimeters.
- Logistics and Warehousing: Keeps sorting machines and conveyors running smoothly by delivering clean, dry air.
In every one of these industries, sloppy air prep can trip up even the fanciest automated line. That’s why big manufacturers turn to suppliers like Omchele, companies that back their powerful FRL units with real-world know-how and dependable technical help.
FRL components may look small beside massive robots and conveyor belts, yet they guard productivity, worker safety, and equipment lifespan. For any B2B firm that runs on automation, choosing solid FRL units is a smart move that strengthens the whole operation.
See for yourself how a reliable partner can tidy up your pneumatic network by visiting Omchele’s complete FRL lineup and browsing air-treatment solutions built for today’s scaled-up factories.